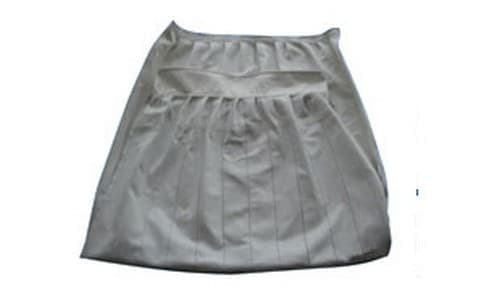
串联磨在技改和调试过程中,我们注意把握了4个环节:①加强通风,由于隔仓板更换为双层筛分隔仓板加上出料篦板篦缝堵焊之后磨机阻力增大、流速降低,此时加强磨机通风,采用合理风量,控制磨内物料的流速,改善粉磨工况尤为重要;②降低漏风率:采用双联锁风阀来降低系统漏风率,克服选粉机在运转过程中扬尘大的缺陷;③调整球锻级配:增大一级磨的平均球径,加大破碎能力,降低二级磨一仓的平均球径,增大研磨能力,同时降低一二级磨二仓研磨体的规格,增加磨机研磨能力,降低系统的循环负荷;④两台磨产量的匹配:由于二级磨入磨物料完全是选粉机选出的中粗粉料,喂料量不能通过微机直接控制,只有通过调整一级磨的出磨细度,来调节选粉机的中粗粉量,进而调节二级磨的中粗粉喂料量。通过试验,只有根据串联磨的特点,将两台磨的球锻级配调整好,出料篦板的篦缝控制6mm左右时,才能有效地控制物料的流速,保证系统产量的平衡。
粉磨系统技改后,通过不断调试实践,获得比较满意技改效果。两台磨的产量由原来的18t/h提高到30t/h,水泥比表面积比原来增加20~30m2/kg,吨粉磨电耗下降了11.4kWh.实行三分离串联粉磨后,进入一级磨的回料全部为150μm以上大颗粒粗粉,不含60~150μm细颗粒,能够有效地消除一级磨粗磨仓的垫层效应,提高粗碎仓的粗碎能力。同时,由于进入二级磨的物料粒度小(60~150μm)且均齐,大大提高二级磨一二仓的研磨能力。实施串联粉磨延长了物料在磨内的停留时间,优化了水泥的颗粒级配组成,改善了水泥性能,产量也得以大幅度提高。但实施串联粉磨之后,两台磨台时产量的匹配还要进一步改进,要通过调整球锻级配、隔仓板的形式和位置等方法来逐步达到产量平衡。